Tekneco #14 - Trigenerazione
Energia: quando arriva il bisogno di freddo
Questa particolare tecnologia che assicura anche la produzione di freddo è utilizzata da svariate industrie in Italia e anche dagli aeroporti
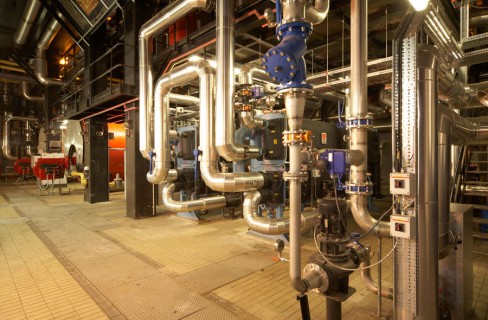
Il recupero del calore assicurato dai sistemi cogenerativi è importante, ma in svariate occasioni più che di “caldo” si ha bisogno di “freddo”. Basti pensare alle celle frigorifere necessarie per la conservazione dei prodotti alimentari. Ecco perché, nell’ambito dei sistemi di cogenerazione, un’applicazione che sta incontrando sempre maggiore interesse e curiosità è quello della trigenerazione. Si tratta, per l’appunto, di una particolare tecnologia che, oltre all’autoproduzione di energia elettrica, consente di utilizzare l’energia termica recuperata anche per la produzione di energia frigorifera, oppure di acqua refrigerata per il condizionamento o i processi industriali.
Da un punto di vista tecnologico, la trigenerazione non comporta grandi complessità: un impianto di questo tipo, essenzialmente, è costituito da un classico cogeneratore combinato con un chiller ad assorbimento, ossia una macchina in grado di produrre energia frigorifera utilizzando il calore come fonte primaria. Per il funzionamento del gruppo frigo ad assorbimento servono due fluidi: il refrigerante e la soluzione assorbente. Le coppie di fluidi più utilizzate sono acqua e ammoniaca, maggiormente impiegata per raggiungere condizioni di raffreddamento con basse temperature (sotto i 0 °C), tipiche dei sistemi di refrigerazione industriale. Dove, invece, non sono necessarie temperature sotto lo zero si usa la combinazione di acqua e bromuro di litio.
I vantaggi della trigenerazione sono molteplici: innanzitutto, l’impiego del calore utile prodotto dall’impianto di cogenerazione, anche per il raffrescamento, permette di massimizzare lo sfruttamento dell’energia termica, rendendo conveniente un utilizzo dell’impianto per un numero maggiore di ore all’anno. Infatti, anche se il rendimento di un chiller ad assorbimento è inferiore rispetto a quello dei tradizionali chiller elettrici, il vero vantaggio è quello di sfruttare il calore prodotto dalla cogenerazione anche nel periodo estivo quando, altrimenti, sarebbe disperso inutilmente nell’ambiente.
Un altro beneficio è più di carattere sistemico: grazie a questa tecnologia, si può ridurre il carico di domanda sulla rete elettrica nazionale dovuto al condizionamento estivo, particolarmente importante in un Paese dal clima mediterraneo come l’Italia. Senza contare, ovviamente, il risparmio energetico, che la trigenerazione può assicurare in misura significativa: un impianto tradizionale, a parità di energia elettrica e frigorifera prodotte, consuma almeno il 17% in più di fonte primaria. Inoltre, i rendimenti e le economie di scala possono essere persino superiori in determinati contesti: basti pensare, ad esempio, ad un ipermercato dove di norma coesistono, nello stesso momento, rilevanti e costanti esigenze di elettricità, energia frigorifera per il condizionamento e termica per il riscaldamento.
Tutto questo spiega perché, in particolare misura negli ultimi anni, questa applicazione abbia iniziato a diffondersi concretamente anche nel nostro Paese: ad esempio il noto pastificio Garofalo, in provincia di Napoli, ha recentemente installato presso il proprio stabilimento un impianto di questo tipo, capace di funzionare per 8.000 ore l’anno, per un rendimento energetico complessivo dell’85% del fabbisogno. L’energia elettrica è interamente autoconsumata dall’edificio industriale, con controllo del generatore in modalità scambio zero con la rete per evitare la cessione di energia quando nelle ore notturne il pastificio non è in piena attività.
Ma anche l’energia termica è completamente utilizzata dalle utenze del pastificio: l’acqua surriscaldata o refrigerata è coinvolta nel processo di produzione della pasta (alimento trafile, termoregolazione dei locali di produzione della pasta), inoltre, una parte dell’acqua calda viene impiegata per il riscaldamento dei locali nei mesi invernali. Per il contenimento delle emissioni inquinanti il gruppo elettrogeno si avvale di differenti tecnologie per la prevenzione della formazione di sostanze inquinanti, attraverso un sistema di regolazione sulla combustione. Anche l’Azienda ospedaliera di Perugia ha puntato sulla trigenerazione per la struttura di Santa Maria della Misericordia: in questo caso l’impianto – alimentato a metano – produce calore per il periodo invernale, energia frigorifera per il periodo estivo ed energia elettrica per totale autoconsumo dell’Azienda ospedaliera. Una soluzione che dovrebbe garantire un taglio di emissioni nell’atmosfera pari a 4.825 ton/anno e 1.189 Tep (tonnellate equivalenti di petrolio) risparmiate.
Anche Plastopiave, azienda veneta attiva da oltre 50 anni nel settore del packaging in plastica e specializzata in contenitori soffiati per tutti i principali ambiti merceologici, ha scelto la trigenerazione di Spark Energy per il sito produttivo dell’azienda a Conegliano (Treviso). L’industria dello stampaggio della plastica ha bisogno di riscaldamento per effettuare la stampa, ma anche di raffreddamento (una volta prodotto il flacone). Altro caso è quello dell’azienda Curti, costruttrice storica nel territorio imolese di macchine e attrezzature per i settori industriali e agricolo, oggi specializzata nella realizzazione di macchine per il packaging. Il continuo aumento dei consumi energetici ha spinto l’azienda a investire sull’autoproduzione energetica: 2G ha così installato un modulo di cogenerazione KWK 200 EG a gas naturale basato su di un motore Man con una potenza di 200 kW elettrico e di 256 kW termico. I 600.000 kWhe prodotti annualmente hanno ridotto del 52% il prelievo di corrente elettrica dalla rete esterna.
Per rendere ancora più efficiente l’impianto con la trigenerazione, Curti ha optato per l’acquisto di un assorbitore da 157 kWfr capace di sfruttare l’energia termica messa a disposizione dal motore anche nei mesi estivi per la produzione di aria fredda a servizio degli ambienti di lavoro (in particolare del reparto saldatura), così da ridurre il tempo di ritorno dell’investimento. Oltre alle industrie, negli ultimi anni la trigenerazione ha conosciuto una notevole diffusione presso molti aeroporti italiani; questo tipo di utenze, in effetti, presentano i requisiti ottimali per il soddisfacimento di richieste simultanee di energia elettrica, termica e frigorifera, assicurando un maggiore rendimento della combustione rispetto alle grandi centrali termoelettriche e l’ottimizzazione di fumi e calore di scarico che altrimenti andrebbero perduti. Già dal 1998 Sea Energia ha adottato una soluzione di questo tipo per lo scalo di Malpensa (Milano) e, a partire dal 2007, anche per l’aerostazione di Linate. Il calore prodotto da quest’ultima, tra l’altro, è anche utilizzato per fornire teleriscaldamento a un’ampia area urbana posta nel contesto territoriale di Milano-Est.
Condividi
Tag
L'autore

Gianluigi Torchiani
Giornalista classe 1981, cagliaritano doc ormai trapiantato a Milano dal 2006. Da diversi anni si interessa del mondo dell’energia e dell'ambiente, con un particolare focus sulle fonti rinnovabili
Ultimi articoli
Più letti della settimana
Come scegliere una stufa a pellet : Consumi, costi e dati tecnici sono i parametri riportati sull’etichetta dell’apparecchio e le caratteristiche della stan...
NovaSomor vince la prima edizione del Klimahouse Startup Award : La startup di Rimini ha ideato un motore solare termodinamico a bassa temperatura applicato al sollevamento delle acque...
Tutti gli studi : ...
Amianto, quando la minaccia si nasconde in casa : Chi chiamare se sospettiamo di avere manufatti o coperture in cemento-amianto a casa nostra...
Pellet di qualità, istruzioni per l’acquisto : Quali sono i parametri utili per il consumatore all’acquisto del pellet? Qualità, innanzitutto, ma anche la lettura dell...