Risparmio energetico
L’efficienza industriale passa dai motori
Le normative europee disciplinano l’introduzione sul mercato di motori ad alta efficienza per abbattere i consumi energetici del settore industriale
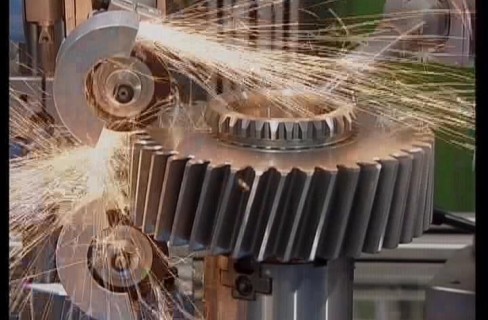
L’elevato costo dell’energia rappresenta uno dei problemi principali per il settore industriale nazionale che, non a torto, si lamenta di continuo del gap esistente con gli altri Paesi europei. In realtà, però, una strada per diminuire la bolletta esiste e si chiama efficienza energetica che, nel settore industriale, è strettamente correlata con il tipo di motori impiegati nel processo produttivo.
Più nel dettaglio, i motori elettrici impiegati nel settore secondario nazionale consumano circa il 75% dell’intero fabbisogno elettrico del sistema industriale. I motori, del resto, si ritrovano praticamente in tutte le applicazioni e i processi, nonché nei sistemi di condizionamento e ventilazione e nei circuiti idraulici collegati a ventilatori e pompe.
È evidente, quindi, che una scarsa efficienza degli stessi si ripercuote in modo considerevole sui costi energetici aziendali. D’altronde, se si considera il ciclo di vita complessivo di un motore industriale (tipicamente superiore a 10 anni), il 98% dei suoi costi dipende dal consumo di energia elettrica, mentre soltanto il 2% è dato dalla spesa iniziale (acquisto più installazione) e dalla manutenzione.
Le possibilità per l’industria di diminuirne i consumi sono essenzialmente di due tipi: dotarsi di motori più efficienti oppure ottimizzare il funzionamento di quelli già esistenti. Nel primo caso occorre attenersi al regolamento europeo 640/2009, che ha stabilito delle precise scadenze temporali per la progressiva introduzione sul mercato di motori ad alta efficienza e il divieto di immissione sul mercato di motori energeticamente inefficienti.
In particolare, dal 16 giugno 2011 i nuovi motori che entrano in funzione in Europa devono avere come minimo un livello di efficienza IE2. A partire dal primo gennaio 2015 tutti i motori con una potenza nominale compresa tra 7,5 e 375 kW dovranno avere come standard minimo il livello di efficienza IE3, oppure il livello di efficienza IE2 e in questo caso essere muniti di variatore di velocità (inverter). Una nuova svolta è prevista dal primo gennaio 2017, quando anche i motori con una potenza nominale compresa tra 0,75 e 375 kW dovranno possedere come minimo il livello di efficienza IE3, oppure il livello di efficienza IE2 ed essere dotati di inverter.
Proprio gli inverter, ossia i sistemi di controllo della frequenza, rappresentano la seconda alternativa a disposizione delle nostre industrie, perché consentono di ridurre in modo considerevole il consumo energetico, soprattutto nel campo delle potenze elevate. L’inverter, infatti, è in grado di variare il numero di giri dei motori in funzione delle reali esigenze, evitando così il funzionamento alla massima potenza quando non necessario, garantendo risparmi significativi (anche nell’ordine del 50%).
Condividi
Tag
L'autore

Gianluigi Torchiani
Giornalista classe 1981, cagliaritano doc ormai trapiantato a Milano dal 2006. Da diversi anni si interessa del mondo dell’energia e dell'ambiente, con un particolare focus sulle fonti rinnovabili
Ultimi articoli
Più letti della settimana
Come scegliere una stufa a pellet : Consumi, costi e dati tecnici sono i parametri riportati sull’etichetta dell’apparecchio e le caratteristiche della stan...
NovaSomor vince la prima edizione del Klimahouse Startup Award : La startup di Rimini ha ideato un motore solare termodinamico a bassa temperatura applicato al sollevamento delle acque...
Tutti gli studi : ...
Amianto, quando la minaccia si nasconde in casa : Chi chiamare se sospettiamo di avere manufatti o coperture in cemento-amianto a casa nostra...
Pellet di qualità, istruzioni per l’acquisto : Quali sono i parametri utili per il consumatore all’acquisto del pellet? Qualità, innanzitutto, ma anche la lettura dell...