ricerca e sviluppo
Social Housing, l’Università di Trento sperimenta costruzioni in acciaio e legno
La struttura, costruita in scala reale, ha dimostrato un’alta capacità di resistenza
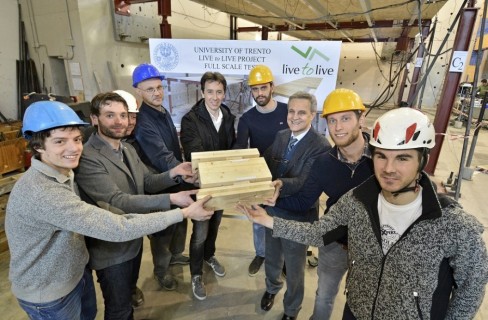
Prova di carico superata. Il test si è tenuto a Mesiano, nel Laboratorio Prove Materiali e Strutture dell’Università di Trento, nell’ambito del progetto di ricerca industriale finanziato dalla Provincia autonoma di Trento attraverso un fondo pubblico per lo sviluppo e la valorizzazione delle risorse territoriali. La struttura in acciaio e legno, costruita in scala reale, ha dimostrato un’alta capacità di resistenza e stabilita ai carichi laterali ai quali è stata sottoposta. Prove con le quali i ricercatori hanno voluto simulare alcune delle sollecitazioni (da scosse sismiche a eventi atmosferici violenti e imprevedibili) alle quali un edificio può essere esposto durante la sua vita utile.
«È un risultato importante» commenta Cristiano Loss, ingegnere e assegnista di ricerca che lavora al Dipartimento di Ingegneria civile, ambientale e meccanica (DICAM) dell’Università di Trento (vedi foto). «Si tratta di una prova sperimentale su una tecnologia costruttiva innovativa che si avvale di componenti verticali e orizzontali appositamente sviluppati e studiati durante gli ultimi tre anni della mia ricerca, sotto la supervisione dei professori Maurizio Piazza e Riccardo Zandonini e dedicata a nuove soluzioni per il Social Housing, l’abitare sociale».
Loss racconta come si sviluppa il progetto: «In questo sistema costruttivo innovativo ibrido acciaio-legno modulare e prefabbricato vengono proposti solai ultraleggeri e resistenti per la realizzazione di nuovi edifici sostenibili. Vengono sviluppate alcune soluzioni di collegamento per la realizzazione e la posa in opera di solai composti acciaio-legno, una prima assoluta che va ad aggiungersi ai già noti sistemi composti per l’edilizia residenziale. La ricerca e la definizione dei collegamenti è stata supportata da analisi numeriche e da prove sperimentali con test eseguiti su componenti di solaio adeguatamente dimensionati. Le indagini hanno consentito di definire e ottimizzare il sistema composto, migliorando lo sfruttamento dei materiali e dei collegamenti. Lo studio ha inoltre consentito di proporre un prototipo di solaio altamente ingegnerizzato. Il sistema è attualmente in evoluzione».
A fare la differenza rispetto al passato è il mix di materiali impiegato nel nuovo tipo di struttura: acciaio, un materiale facilmente riciclabile, e legno di abete, un materiale naturale di grande qualità prodotto sul territorio trentino. Ma anche la grande flessibilità della struttura, che libera spazi sempre più ampi per la progettazione degli interni rendendo possibile, ad esempio, spostare le pareti interne assecondando le esigenze d’uso. Una caratteristica importante specialmente nell’edilizia sociale, dove nel tempo può capitare di dover adattare lo stesso appartamento per ospitare famiglie più o meno numerose.
«Il superamento del test di resistenza eseguito oggi su una costruzione in scala reale – spiega Loss – rappresenta una tappa importante per sviluppare prototipi di edilizia abitativa sociale. Un modello nel quale convergano alto contenuto tecnologico, adattabilità a diversi ambiti territoriali, flessibilità alle esigenze, leggerezza e robustezza, sostenibilità ambientale, attenzione per la dimensione sociale, un prodotto di qualità a costi accessibili (nell’ordine dei mille euro a metro quadro). È ciò che stiamo facendo con il progetto “livetolive” per rispondere a una domanda che è insieme sociale, economica, tecnologica ed ambientale».
Il progetto fissa però anche un altro importante tassello nella collaborazione tra università e mondo produttivo. A sostenere il progetto triennale e ad accompagnarlo al traguardo della realizzazione e prossimamente commercializzazione del prodotto è stata Premetal, azienda di Rovereto che da anni si occupa di edilizia prefabbricata. «Quello di oggi è per noi è un risultato molto importante – commenta Andrea Poli, responsabile Ricerca e Sviluppo – perché permette alla nostra azienda di acquisire un ulteriore vantaggio competitivo. Questa soluzione ibrida acciaio-legno, la prima mai realizzata in questo campo, consente di abbattere i costi della posa in opera e allo stesso tempo minimizza il rischio di infortuni o problemi di varia natura in cantiere, perché le varie componenti vengono prodotte in stabilimento e poi assemblate in loco con grande riduzione dei tempi. Con questa tecnologia abbiamo stimato di riuscire a consegnare un edificio di quattro piani in sei-otto mesi di cantiere. Pensiamo di avviare la commercializzazione dal prossimo autunno».
Condividi
Tag
L'autore

Redazione Web
Ultimi articoli
Più letti della settimana
Come scegliere una stufa a pellet : Consumi, costi e dati tecnici sono i parametri riportati sull’etichetta dell’apparecchio e le caratteristiche della stan...
NovaSomor vince la prima edizione del Klimahouse Startup Award : La startup di Rimini ha ideato un motore solare termodinamico a bassa temperatura applicato al sollevamento delle acque...
Tutti gli studi : ...
Amianto, quando la minaccia si nasconde in casa : Chi chiamare se sospettiamo di avere manufatti o coperture in cemento-amianto a casa nostra...
Pellet di qualità, istruzioni per l’acquisto : Quali sono i parametri utili per il consumatore all’acquisto del pellet? Qualità, innanzitutto, ma anche la lettura dell...
Commenti
È stato inserito 1 commento.