Sperimentazione e sviluppo di impianti di refrigerazione ecosostenibili
Il calore rappresenta un ingrediente fondamentale nello sviluppo sociale e tecnologico dell’uomo. La possibilità di produrre calore ha infatti permesso al genere umano di riscaldarsi in condizioni ambientali avverse nonché di migliorare la propria alimentazione mediante la cottura dei cibi. Successivamente, la combustione ha consentito la locomozione non animale, l’industrializzazione e la produzione di energia elettrica fino a tutti gli sviluppi tecnologici ormai entrati a far parte della vita quotidiana.
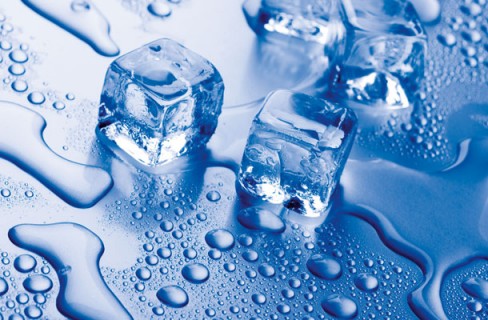
Photo: sebastian Duda@fotolia
L. A. CATALANO, F. DE BELLIS, R. AMIRANTE Dipartimento di Ingegneria Meccanica e Gestionale, Politecnico di Bari
U. AYR Dipartimento di Architettura e Urbanistica, Politecnico di Bari
Il calore rappresenta un ingrediente fondamentale nello sviluppo sociale e tecnologico dell’uomo. La possibilità di produrre calore ha infatti permesso al genere umano di riscaldarsi in condizioni ambientali avverse nonché di migliorare la propria alimentazione mediante la cottura dei cibi. Successivamente, la combustione ha consentito la locomozione non animale, l’industrializzazione e la produzione di energia elettrica fino a tutti gli sviluppi tecnologici ormai entrati a far parte della vita quotidiana.
Se la generazione controllata di calore da parte dell’uomo si può far risalire a tempi molto antichi (Preistoria), il contrario, cioè la sottrazione di calore, è una tecnologia scoperta ed utilizzata in tempi notevolmente più recenti. Storicamente infatti, non si conoscevano tecniche in grado di produrre il freddo a piacimento a partire da qualsiasi condizione, ma ci si limitava a preservare il freddo “naturale” isolandolo il più possibile dalle fonti di calore. La conservazione dei cibi a basse temperature avveniva in luoghi riparati dalla radiazione solare e ad alto isolamento termico come cantine o cisterne oppure adoperando ghiaccio o neve prelevati ad alta quota e trasportati a caro prezzo dove necessario.
Scientificamente, la differenza alla base di questo ritardo tecnologico si può spiegare considerando che la sottrazione di calore comporta una locale riduzione di entropia (si ricorda che il secondo principio della termodinamica afferma che l’entropia totale di un sistema isolato non può che aumentare o al massimo mantenersi costante). Tale principio conduce a due conseguenze: la prima è che per poter sottrarre calore da un sistema bisogna aumentare l’entropia totale più della diminuzione locale dovuta al raffreddamento; mentre la seconda è che la fisica stabilisce una scala ben precisa: aumentare l’entropia (producendo calore, ad esempio) è semplice, diminuirla, seppur localmente (sottraendo calore, ad esempio), è molto più difficile. Banalizzando, si potrebbe dire che sottrarre calore equivale a muoversi controcorrente; da qui le difficoltà riscontrate nel corso dei secoli e risolte solo a partire dal XIX secolo.
Le prime “macchine del freddo” furono brevettate verso la metà del 1800 e sfruttavano l’evaporazione a pressione costante di gas ad alta volatilità come ammoniaca, biossido di zolfo ed etere etilico; tali gas tuttavia presentavano il notevole svantaggio di non essere sicuri in quanto infiammabili e tossici.
Un’altra possibilità esplorata fin dalla seconda metà del XIX secolo si basava sulla riduzione di temperatura conseguente all’espansione di aria in una macchina alternativa, sulla base del funzionamento delle macchine a vapore (Figura 1).
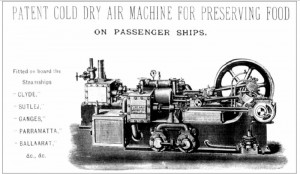
Fig. 1 – La macchina per la refrigerazione ad aria, a bordo di navi passeggeri, costruita all’incirca nel 1890 dalla “J.& E. Hall”.
Tali macchine erano caratterizzate da ottima sicurezza ed affidabilità (vennero infatti impiegate sulle navi da trasporto), ma anche da rendimenti bassi nonché da alcuni problemitecnici quali ingombro e manutenzione. Di conseguenza, nel tempo furono preferite le macchine ad evaporazione (vapor-compression refrigerators) e fino agli anni ’30 del 1900 la gran parte della macchine frigorifere conteneva ammoniaca quale fluido di processo. Una serie di incidenti mortali dovute all’esplosione del gas spinse la ricerca ad individuare una nuova classe di gas non pericolosi per l’uomo in grado di sostituire l’ammoniaca. La scelta ricadde sul Freon, nome commerciale (brevetto DuPont) di un gas che all’epoca sembrava la soluzione perfetta al problema, vista la sua bassa tossicità, infiammabilità e reattività chimica. Fu solo a partire dagli anni ’70 del XX secolo che fu sollevato il problema dell’interazione di questo gas con l’ozono atmosferico, provocandone il rapido assottigliamento. I componenti del Freon, i cloro-fluoro-carburi (CFC) assieme alla sottoclasse degli idro-cloro-fluoro-carburi (HCFC) furono messi al bando con il protocollo di Montreal nel 1987 in quanto sostanze responsabili dell’impoverimento dell’ozono (ODP, Ozone Depleting Substances) e sostituiti negli impianti frigoriferi dagli idro-fluoro-carburi (HFC) e dagli per-fluoro-carburi (PFC), tuttora utilizzati.
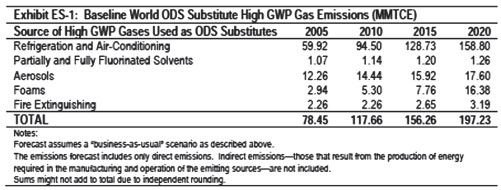
Tab. 1 – Valori del potenziale di riscaldamento globale (GWP) dei principali gas correntemente utilizzati per la refrigerazione secondo l’IPCC.
Contesto attuale: problemi relativi ai refrigeranti di comune impiego
Sembrerebbe tutto risolto, ma non è così: anche questi ultimi gas sono dannosi per l’atmosfera, precisamente sono considerati da centinaia a migliaia di volte più pericolosi del biossido di carbonio (CO2) nel contribuire all’effetto serra, ossia al riscaldamento del pianeta. In Tabella 1 sono riportati i valori del potenziale riscaldamento globale (GWP, Global Warming Potential) indotti dall’emissione dei gas correntemente utilizzati per la refrigerazione, così come stimati dall’IPCC, l’Intergovernmental Panel on Climate Change.
In aggiunta, la permanenza di questi gas nell’atmosfera è di alcune decine anni; ad esempio il refrigerante noto come HFC-143a, uno dei più usati, ha un GWP di 3800 ed una permanenza nell’atmosfera di 52 anni [2]. Si capisce quindi come il problema di mitigare o addirittura eliminare l’emissione di gas ad alto GWP sia di grande rilevanza ed attualità, soprattutto considerata la quantità di emissioni previste dall’agenzia statunitense EPA (Environmental Protection Agency) e riportate in Tabella 2 [3]. Come chiaramente riportato nella tabella, il settore della refrigerazione e del condizionamento (genericamente: produzione del freddo) è responsabile da solo di circa l’80% dell’emissione totale di gas ad alto potenziale di riscaldamento globale, per giunta in forte crescita: l’EPA stima infatti un aumento di 30 milioni di tonnellate equivalenti di anidride carbonica ogni cinque anni (l’emissione avviene sia alla dismissione degli impianti sia attraverso perdite e trafilamenti stimati su base annua, infatti gli impianti necessitano di “ricariche” periodiche di gas). Tale incremento è dovuto principalmente all’aumento di impianti operanti su scala globale, soprattutto nei paesi in via di sviluppo.
Il già citato rapporto dell’IPCC [2] fornisce una stima più precisa ed aggiornata delle emissioni, dividendole per classi di inquinanti (Figura 2) e confrontando lo scenario reale del 2002 con le previsioni relative al 2015 nell’ipotesi di livello tecnologico degli impianti costante (Business As Usual, BAU). Il grafico fornisce una serie di informazioni interessanti: la prima è che complessivamente le emissioni si riducono leggermente, ma ciò è dovuto alla riduzione della quota parte dei CFC che, sebbene al bando da tempo, continuano ad essere emessi dagli impianti già in funzione nel 1987 e dai paesi che non hanno aderito al protocollo. La seconda considerazione che emerge dalla Figura 2 è che, pur diminuendo le emissioni di CFC dannosi per l’ozono, aumentano significativamente gli HFC, cioè la nuova generazione di gas usati negli attuali impianti di refrigerazione che non danneggiano l’ozono ma che incrementano l’effetto serra.
In sintesi, gli impianti di refrigerazione moderni pur non danneggiando l’ozono atmosferico emettono gas ad alto potenziale di riscaldamento globale (fino a migliaia di volte il valore dell’anidride carbonica), sono da soli responsabili di circa l’80% delle emissioni di tali gas e le previsioni stimano un forte incremento delle emissioni responsabili dell’aumento dell’effetto serra del nostro pianeta.
Esistono quindi una serie di ragioni ambientali e di sostenibilità che giustificano lo sforzo continuo della ricerca scientifica per fornire valide alternative (anche dal punto di vista economico) alla tecnologia alla base degli impianti esistenti.
Il ciclo ad aria, una possibile alternativa
Alla luce delle problematiche ambientali precedentemente esposte, lo studio di cicli e di impianti di refrigerazione “sostenibili” differenti dai tradizionali vapor-compression è molto attuale. Una disamina completa delle varie tecnologie disponibili, di quelle oggetto di ricerca, delle problematiche e dei vantaggi di ognuna è al di fuori dello scopo del presente lavoro, ma è disponibile consultando la referenza [4].
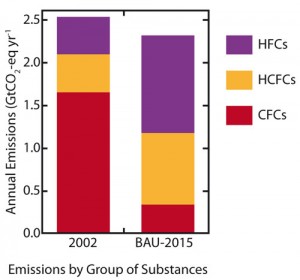
Fig. 2 – emissione di gas dannosi per l’atmosfera da impianti di refrigerazione secondo l’IPCC: dati 2002 e previsioni 2015 nello scenario business-As-Usual (bAU).
In questa sede invece si analizza il ciclo ad aria, vale a dire la tecnologia che per prima fu pensata come alternativa per la produzione artificiale del freddo (cfr. il paragrafo “Cenni Storici”). Il ciclo ad aria infatti, come suggerito dal nome stesso, adopera esclusivamente aria come fluido operante e non emette nessun altro gas inquinante o dannoso per l’ambiente; qualora estensivamente utilizzato, permetterebbe quindi una drastica riduzione dei gas serra emessi dagli impianti attuali. Esso si basa sull’espansione dell’aria preceduta da una compressione e può essere a ciclo aperto (aria prelevata, processata e poi scaricata) o a ciclo chiuso (la stessa quantità di aria opera in continuo subendo trasformazioni cicliche); a seguito dell’espansione, la temperatura diminuisce fino a valori molto bassi. In questo modo, l’aria può essere utilizzata per refrigerare un ambiente mentre il lavoro prodotto durante l’espansione è di solito adoperato per sostenere parte della compressione.
Dopo gli esordi nella seconda metà del XIX secolo, il ciclo ad aria è stato utilizzato in tempi moderni per la refrigerazione dell’aria destinata ai passeggeri degli aerei (in particolar modo militari) per ragioni di peso ridotto e semplicità costruttiva. Pur essendo stato riconosciuto la tecnologia più promettente a lungo termine per sostituire gli impianti tradizionali [4], non si è diffuso su larga scala ad impianti stazionari a causa dell’incertezza sulle sue prestazioni (sebbene esistano ditte che ne commercializzino alcune versioni).
Nel 1998, Fleming ed altri autori [5,6] hanno studiato l’applicazione del ciclo ad aria per scopi di riscaldamento e refrigerazione contemporaneamente, giungendo alla conclusione che tale ciclo deve essere accuratamente progettato vista la sua bassa efficienza. Due anni più tardi l’istituto olandese TNO (Institute of Environmental Sciences, Energy Research and Process Innovation) ha presentato un rapporto molto dettagliato riguardante la sperimentazione e lo studio di un proprio prototipo di ciclo ad aria [7]. Gli autori del report hanno dapprima analizzato le potenzialità del ciclo ad aria (includendo anche le soluzioni commerciali già esistenti) per poi costruire e testare un impianto pilota progettato per il riscaldamento, la ventilazione ed il condizionamento degli edifici.
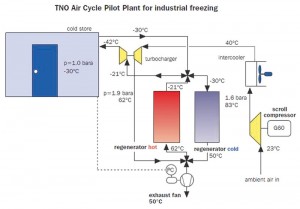
Fig. 3 – Impianto di refrigerazione ad aria per il congelamento testato presso i laboratori della TNO
Nel loro studio essi dimostrano la fattibilità pratica di tale ciclo così come la sua semplicità, che si traduce da un lato in affidabilità e dall’altro in economia e facilità di manutenzione. Lo stesso istituto ha anche realizzato un impianto di congelamento rappresentato schematicamente in Figura 3 e funzionante secondo un ciclo aperto recuperativo. Una compressione bistadio interrefrigerata produce un flusso di aria a circa due bar assoluti che arriva nella turbina di un turbogruppo dopo essere stata ulteriormente raffreddata attraverso il passaggio in un recuperatore. L’aria a bassa temperatura in uscita dalla turbina è convogliata nella cella di congelamento, da cui poi passa al recuperatore prima di essere scaricata nell’ambiente. Il prototipo può produrre aria a -50°C con un COP (Coefficient of Performance) di 0.72 [7,8]; tuttavia, gli autori hanno calcolato che il ciclo ad aria può essere realmente competitivo con i cicli di tipo vapour compression con l’utilizzo di compenenti costitutivi a più alta efficienza (specialmente la turbina). Anche il recuperatore ha una grande influenza sulla performance generale del ciclo e deve essere progettato “ad hoc”.
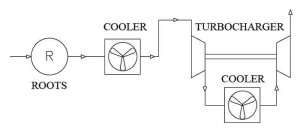
Fig. 4 – Layout dell’impianto sperimentale testato presso i Laboratori della Sezione di Macchine ed Energetica del Dipartimento di Ingegneria Meccanica e Gestionale.
Le potenzialità del ciclo ad aria sono state studiate anche per il trasporto su strada (specialmente alimentare) [9], e giudicato di nuovo promettente, pur con una bassa efficienza dovuta alle specifiche delle macchine utilizzate. Spence ed altri autori [10, 11] hanno sperimentato un impianto con all’incirca lo stesso layout proposto dalla TNO ma di dimensioni sufficientemente ridotte da essere contenuto nell’unità di refrigerazione di un comune autocarro per il trasporto di alimenti deperibili. Il risultato della sperimentazione è stato una efficace refrigerazione ma al prezzo di un consumo di combustibile troppo elevato. Sulla base dei rilievi sperimentali tuttavia, gli autori sono stati in grado di identificare le maggiori carenze (nello specifico: le efficienze delle turbomacchine e degli scambiatori di calore) e quindi di prevedere numericamente che un ciclo ad aria ottimizzato ha le capacità per “equiparare il consumo di combustibile di un’unità di refrigerazione per autotrasporto, fornendo però il beneficio di emissioni di gas refrigerante pari a zero” [11], specialmente a carico parziale di esercizio.
Di recente, il ciclo ad aria è stato applicato ad un impianto di raffrescamento-deumidificazione [12], con risultati migliori dei sistemi di essiccazione tradizionali.
Scopo di questo lavoro è aumentare lo stato dell’arte riguardo la tecnologia del ciclo ad aria con la proposta di un nuovo layout in grado di aumentare l’efficienza dei componenti, ossia migliorando il fattore limitante nelle progettazioni citate precedentemente.
La prossima sezione descrive l’apparato di test impiegato per condurre una campagna sperimentale volta alla comprensione dei principali punti critici riscontrati negli studi passati. A partire da questa analisi preliminare, nella sezione successiva è descritto il nuovo layout proposto, assieme alla stima delle sue performance per mezzo di simulazioni numeriche basate sulle equazioni della termodinamica. Infine, alcune conclusioni sul lavoro svolto sono presentate nell’ultima sezione.
Impianto Sperimentale e Risultati Preliminari
Il ciclo ad aria impiegato per la sperimentazione è rappresentato in Figura 4: l’aria prelevata dall’ambiente è inizialmente compressa da una soffiante di tipo Roots (scelta per via della sua disponibilità presso il Laboratorio di Macchine ed Energetica del Politecnico di Bari); successivamente, uno scambiatore aria-aria (cooler) ripristina la temperatura ambiente prima che il flusso sia ulteriormente compresso dal turbocompressore centrifugo di un turbogruppo automobilistico. La compressione è interrefrigerata per due ragioni: per ridurre il lavoro di compressione richiesto dal compressore centrifugo e per mantenere una temperatura relativamente bassa anche al termine della seconda compressione. Prima dell’ingresso in turbina il flusso di aria è nuovamente raffreddato fino alle condizioni ambiente; l’espansione seguente è quindi in grado di produrre un flusso di aria a bassa temperatura. Questo tipo di soluzione impiantistica è più semplice rispetto a quelle analizzate dagli autori su menzionati in quanto non è presente il recuperatore.
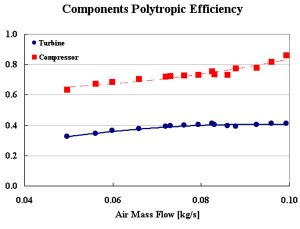
Fig. 6 – Efficienze politropiche del compressore centrifugo e della turbina centripeta misurate nell’impianto sperimentale.
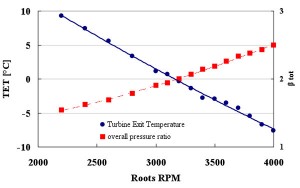
Fig. 7 – Temperatura in uscita turbina (blu) e rapporto totale di espansione (rosso) misurati sull’impianto.
Sebbene questa configurazione limiti la temperatura dell’aria in uscita dalla turbina a valori non troppo bassi, va ricordato che lo scopo di questa analisi preliminare è quello di rilevare le principali problematiche del ciclo in generale e non di sviluppare un impianto di refrigerazione ottimale. Di conseguenza, anche la configurazione scelta può essere considerata adatta alla scopo e preferita a layout più complessi considerata la sua semplicità. La Figura 5 mostra il cuore dell’apparato sperimentale, il turbogruppo (in grigio nel quadrante in basso a sinistra), assieme a parte della strumentazione impiegata. Il turbogruppo impiegato nel presente studio è il Garrett GT1541 dotato di valvola Wastegate (bloccata), montato di solito su motori automobilistici di piccola cilindrata (1300 cm3).
Praticamente tutti gli autori che hanno studiato il ciclo ad aria in passato hanno rilevato che le efficienze delle turbomacchine sono il fattore limitante per l’efficienza del ciclo stesso [5-11]. Uno dei principali obiettivi del presente studio è quello di misurare le efficienze del compressore centrifugo e della turbina centripeta del turbogruppo. L’apparato sperimentale è composto da termocoppie di tipo K e T, trasduttori di pressione e un misuratore di portata della Elster Instromet.
Le misure rappresentate in Figura 6 mostrano chiaramente che la turbina espande l’aria con una bassa efficienza operativa (compresa tra 0.3 e 0.4), mentre il compressore dimostra un comportamento migliore, soprattutto alle alte portate. Un’efficienza della turbina così bassa non è accettabile in quanto si traduce in un minor lavoro estratto, con la conseguenza di una temperatura più alta alla fine dell’espansione ed un basso rapporto di compressione nel centrifugo.
In aggiunta, la turbina opera in condizioni distanti dal suo punto di massima efficienza, che il costruttore dichiara essere pari a 0.65 circa. La Figura 7 fornisce un’idea precisa degli effetti di una bassa efficienza di espansione: la temperatura in uscita turbina (Turbine Exit Temperature, TET, in blu) è sempre al di sopra di -10° C, anche ad alte portate, ed il rapporto di espansione totale (in rosso) è relativamente basso a causa del ridotto incremento di pressione nel compressore centrifugo.
Queste considerazioni indicano che per aumentare l’efficienza del ciclo ad aria dovrebbero essere selezionate migliori condizioni operative di funzionamento delle turbomacchine. In altri termini, non basta impiegare turbogruppi con un’efficienza costruttiva più alta, è necessario anche far operare il turbogruppo in condizioni di alto rendimento. Per far ciò, bisogna imporre un accoppiamento ottimale tra il turbocompressore centrifugo e la turbina già in sede di progettazione dell’impianto. Si tratta di una procedura alquanto diversa dal semplice “innesto” nell’impianto di un turbogruppo automobilistico prodotto per elaborare la stessa portata, a causa delle differenti condizioni termodinamiche in gioco nei due sistemi. Infatti, poiché le pressioni e le temperature di esercizio della turbina in un impianto di refrigerazione differiscono da quelle tipiche motoristiche, la condizione di equilibrio del turbogruppo cadrà molto probabilmente ben lontana dall’ottimo programmato dal costruttore per tutt’altra applicazione. Non sono disponibili sul mercato turbogruppi specificatamente prodotti per l’impiego in impianti di refrigerazione; tuttavia, piuttosto che progettare e produrre una nuova macchina (con costi notevoli), conviene adattare il più possibile l’impianto in modo da avvicinarsi alle condizioni di massimo rendimento del gruppo di sovralimentazione. In questo modo, si trae vantaggio dall’adoperare un componente a basso costo e di ampia disponibilità commerciale poiché di larghissimo impiego nel settore automobilistico.
Infine, va sottolineato come i cuscinetti impiegati nei turbogruppi automobilistici non garantiscano aria completamente oil-free; ciò suggerisce di abbandonare l’idea di impiegare l’aria a bassa temperatura direttamente per il congelamento o la conservazione degli alimenti, così come per tutte le altre applicazioni in cui l’aria deve essere respirata.
Miglioramenti progettuali
Il ciclo ad aria può essere migliorato seguendo due criteri progettuali:
l’imposizione di un abbinamento ottimale tra le condizioni di funzionamento dell’impianto e l’equilibrio meccanico del turbogruppo;
l’impiego di turbogruppi di dimensioni maggiori a parità di portata: l’efficienza infatti cresce al crescere delle dimensioni geometriche delle macchine per ragioni principalmente costruttive.
Il primo criterio mira a garantire che il turbogruppo scelto lavori effettivamente al massimo delle sue potenzialità. Date le mappe dei componenti, in sede di progetto dell’impianto è possibile imporre la portata ed i rapporti di pressione tali da soddisfare questo criterio. Un esempio di questa procedura è visibile in Figura 8, in cui è riportata la mappa del compressore centrifugo del turbogruppo GT1544.
La linea di massima efficienza, in rosso, indica quali coppie ordinate di valori portata/rapporto di compressione è necessario scegliere per far operare il centrifugo ad alto rendimento. Tuttavia, esistono moltissime coppie di punti possibili: la migliore tra queste è quella in grado di massimizzare contemporaneamente l’efficienza di compressore e turbina rispettando alcuni vincoli:
equilibrio meccanico del turbogruppo (il lavoro fornito dalla turbina deve eguagliare il lavoro richiesto dal compressore più il lavoro dissipato nei cuscinetti),
alcune temperature sono fissate dalla presenza degli scambiatori di calore. Ad esempio, la temperatura ambiente è la più bassa temperatura all’ingresso del recuperatore (o all’ingresso della turbina se non viene usato il recuperatore).
La procedura descritta è di natura iterativa: una volta che alcuni parametri progettuali sono stati fissati (portata, temperatura ambiente, ecc.), una variabile di controllo è modificata iterativamente finché non si soddisfano tutte le condizioni e si raggiunge l’ottimo. Le trasformazioni termodinamiche all’interno dei componenti dell’impianto possono essere parametrizzate per mezzo di equazioni zero-dimensionali e l’ausilio delle mappe del turbogruppo.
Il secondo criterio punta alla selezione di un turbogruppo adatto allo scopo ma con efficienze le più alte possibili: a causa delle tolleranze dimensionali di produzione, infatti, i turbogruppi più grandi raggiungono facilmente efficienze di compressione oltre l’80%, e di espansione oltre il 70%. La limitazione è che turbogruppi più grandi richiedono anche portate corrette più grandi, e ciò comporta a sua volta impianti più grandi e costosi. In questo lavoro si propone una soluzione alternativa per ottenere grandi portate corrette: essa consiste principalmente nell’uso indiretto del flusso di aria fredda, che espande fino ad una pressione minima inferiore al valore ambiente.
Sulla scorta dei due criteri progettuali descritti precedentemente si propone un nuovo layout di ciclo ad aria (Figura 9): una prima leggera compressione aumenta la pressione dell’aria prelevata dall’ambiente di pochi decimi di bar; successivamente, il flusso si raffredda passando attraverso uno scambiatore aria-aria ed un recuperatore. All’uscita del recuperatore, l’aria espande in turbina fino ad una pressione inferiore a quella ambiente e temperatura molto bassa, in modo da poter essere impiegata per scopi di refrigerazione (indicati genericamente come “heat transfer” in Figura 9) e poi per abbassare la temperatura in ingresso turbina all’interno del recuperatore.
Infine, si raggiunge nuovamente la pressione atmosferica attraverso un’altra compressione: poiché però il compressore centrifugo non è in grado contemporaneamente di elaborare tutta la portata in uscita dalla turbina e di lavorare ad alto rendimento, si rende necessario l’uso di un secondo compressore in parallelo al turbocompressore. Tale compressore, indicato genericamente come Roots 2 in Figura 9, può essere in realtà un compressore volumetrico a compressione per riduzione di volume per migliorare ulteriormente le performance dell’impianto. Con l’ausilio del secondo compressore volumetrico quindi, il centrifugo elabora una portata corretta inferiore e con rapporto di compressione maggiore, in condizione di massima efficienza. Il layout proposto permette quindi di usare turbogruppi di grandi dimensioni (con i vantaggi citati) in impianti di grandezza contenuta e con compressori di potenza ridotta. In più, tale ciclo può essere progettato per ottimizzare l’abbinamento tra le condizioni di efficienza delle turbomacchine e le condizioni operative tipiche di un impianto di refrigerazione ad aria.
Il ciclo descritto è stato modellizzato per mezzo delle equazioni della termodinamica ed implementato in routine numeriche elaborate al calcolatore ed i risultati ottenuti sono descritti di seguito.
Risultati numerici
Una prima valutazione del nuovo ciclo proposto e dei miglioramenti progettuali è presentata in Figura 10. Il turbogruppo impiegato nelle simulazioni è il Garrett GT22 e l’efficienza frigorifera (COP) è definita dall’espressione seguente:
dove è la portata di aria, Cp è il calore specifico a pressione costante dell’aria, TU è la temperatura costante richiesta dall’utilizzatore, e PBC1 + PBC2 rappresenta la potenza meccanica richiesta dai due compressori volumetrici. La performance del nuovo impianto è soddisfacente: alla fine dell’espansione si può raggiungere una temperatura molto bassa (al di sotto dei -60°C per le alte portate), mentre l’efficienza è all’incirca costante nel range di portata considerato, tranne un leggera diminuzione alle alte portate dovuta all’aumento più che proporzionale del termine PBC2.
Le simulazioni numeriche sono state utilizzate anche per analizzare l’effetto sull’impianto di due importanti parametri: la temperatura di ingresso turbina (Turbine Inlet Temperature, TIT) e la temperatura dell’ambiente in cui l’impianto si trova ad operare. La temperatura di ingresso turbina è strettamente legata alla temperatura richiesta dall’utilizzatore ed il suo effetto è evidenziato in Figura 11: al crescere della TIT (a causa di una più bassa efficienza del recuperatore o per una maggiore potenza termica richiesta dall’utilizzatore) la minima temperatura raggiungibile nell’impianto (TET, in blu) aumenta, così come il COP (in rosso).
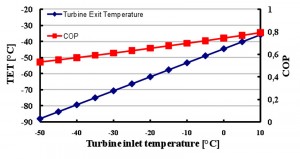
Fig. 11 – Effetto della temperatura in ingresso turbina (TIT) sulla performance globale dell’impianto.
L’effetto del secondo parametro è presentato in Figura 12: al crescere della temperatura ambiente il COP diminuisce leggermente, mentre la temperatura dell’aria in uscita dalla turbina è quasi costante (a parità di tutte le altre condizioni). Ciò è dovuto alla presenza del recuperatore che mantiene invariata la temperatura in ingresso turbina.
Quest’ultimo risultato è di notevole rilevanza, perché dimostra come l’efficienza dell’impianto è poco dipendente dalle condizioni ambientali; in altre parole, contrariamente a quanto accade con i cicli tradizionali a compressione di vapore, il ciclo ad aria mantiene costante la minima temperatura raggiungibile anche in ambienti molto caldi con la stessa potenza fornita (allo stesso costo).
Potrebbe sembrare che l’efficienza del ciclo ad aria fin qui presentato sia più basso di un comune ciclo di tipo vapour-compression, ma valgono alcune considerazioni:
le minime temperature raggiungibili con il ciclo ad aria proposto sono più basse di quelle raggiungibili con i tradizionali cicli a compressione di vapore. Per esempio, l’impianto descritto potrebbe essere usato per applicazioni di congelamento rapido, molto apprezzata nell’industria alimentare;
i rendimenti delle turbomacchine possono essere incrementati impiegando turbogruppi di dimensioni ancora maggiori, in modo da aumentare il COP e diminuire la TET; la competitività del ciclo ad aria proposto rispetto agli impianti vapour-compression aumenta all’aumentare della potenza termica da estrarre (cooling capacity) ed al diminuire della temperatura minima da raggiungere. Sebbene un’analisi economica comparativa sia al di là degli scopi di questo lavoro, è possibile stimare che l’impianto ad aria proposto sia soggetto agli stessi consumi energetici di un impianto tradizionale per alte cooling capacities e temperature molto basse (ad esempio: impianti di congelamento industriali di grossa taglia);
il ciclo ad aria non emette gas inquinanti ad alto potenziale di riscaldamento globale.
Studi futuri saranno condotti su questi aspetti, e particolarmente sull’analisi dei vantaggi ottenibili dall’uso del ciclo ad aria rispetto agli impianti tradizionali, soprattutto in termini economici.
Conclusioni
Nel presente lavoro è stato studiato il ciclo Joule-Brayton inverso (ciclo ad aria) ed una possibile variante, per la realizzazione di impianti di refrigerazione basati sull’uso di turbogruppi di derivazione automobilistica. A partire da studi passati disponibili in letteratura, è stato realizzato e testato presso il Laboratorio di Macchine del Politecnico di Bari un impianto sperimentale al fine di analizzare le problematiche principali che limitano le prestazioni del ciclo ad aria. Si tratta di un impianto a ciclo aperto con una compressione bistadio interrefrigerata ma senza recuperatore. Le misure effettuate hanno rivelato performance non accettabili sia in termini di efficienza che di temperatura minima raggiungibile, principalmente a causa del basso rendimento della turbina.
E’ stato evidenziato l’abbinamento non ottimale tra le condizioni operative di un impianto di refrigerazione e quelle per cui sono stati progettati i turbogruppi automobilistici. E’ stato quindi proposto un nuovo layout basato su due criteri progettuali: 1) l’imposizione di un abbinamento ottimale tra il turbogruppo e l’impianto di refrigerazione, e 2) l’utilizzo di gruppi di sovralimentazione più grandi, in grado di raggiungere efficienze maggiori. In accordo con questi due criteri progettuali è stato simulato al calcolatore un ciclo recuperativo con una pressione minima alla fine dell’espansione inferiore a quella atmosferica. I risultati ottenuti mostrano che il nuovo impianto è in grado di fornire aria a temperatura molto bassa (-60°C ed oltre), rendendolo ideale per applicazioni di congelamento. Inoltre, la presenza del recuperatore rende la temperature in uscita turbina indipendente dalla temperatura ambiente: di conseguenza, il ciclo ad aria proposto può operare anche in ambienti molto caldi (al contrario degli impianti tradizionali di tipo vapour-compression).
Ringraziamenti
Il presente lavoro è stato finanziato dal MIUR, nell’ambito del PRIN 07 “Impianti di refrigerazione ad aria ad elevato COP”.
Commenti
È stato inserito 1 commento.
Rispondi
Condividi
Tag
L'autore

Redazione Web
Ultimi articoli
Più letti della settimana
Come scegliere una stufa a pellet : Consumi, costi e dati tecnici sono i parametri riportati sull’etichetta dell’apparecchio e le caratteristiche della stan...
NovaSomor vince la prima edizione del Klimahouse Startup Award : La startup di Rimini ha ideato un motore solare termodinamico a bassa temperatura applicato al sollevamento delle acque...
Tutti gli studi : ...
Amianto, quando la minaccia si nasconde in casa : Chi chiamare se sospettiamo di avere manufatti o coperture in cemento-amianto a casa nostra...
Pellet di qualità, istruzioni per l’acquisto : Quali sono i parametri utili per il consumatore all’acquisto del pellet? Qualità, innanzitutto, ma anche la lettura dell...
Alberto
scrive il 20 maggio 2014 alle ore 16:57
Salve nell'articolo si legge: Di recente, il ciclo ad aria è stato applicato ad un impianto di raffrescamento-deumidificazione [12], con risultati migliori dei sistemi di essiccazione tradizionali. ma poi la referenza non è indicato il riferimento bibliografico che sarebbe per me molto interessante. Potreste indicarmelo? Grazie per la cortese attenzione. Saluti Alberto Palma